Achievements
R&D Topics
Response to Tighter Environmental Regulations for Automobiles (=Improving Fuel Efficiency)
Solution Styrene Butadiene Rubber (SSBR) for Fuel-Efficient Tires

Achieving Both High Gripping Power and Low Rolling Resistance Using Advanced Rubber Design Technology
SSBR is an essential raw material for the tread of fuel-efficient tires, and demand for the material is growing.
Tire tread is the only part of the tire in contact with the road, so SSBR contributes significantly to braking performance (gripping power) and fuel efficiency (rolling resistance).
To create a fuel-efficient, high-performance tire, it is necessary to achieve both high gripping power and low rolling resistance (making rolling easier), which are contradictory performance attributes. Advanced technological capabilities are also required for manufacturing.
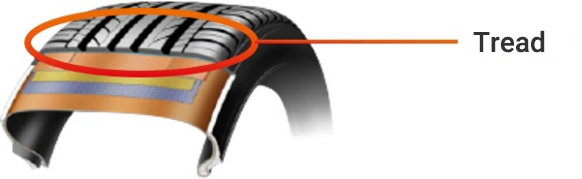
ENEOS Materials' SSBR has outstanding processability and fuel-efficient properties, and is rated highly in Japan and overseas as a raw material for fuel-efficient tires.
Contributions to the Improvement of EV (Electric Vehicle) Performance
Lib Battery Binder for Automotive Use / TRD®
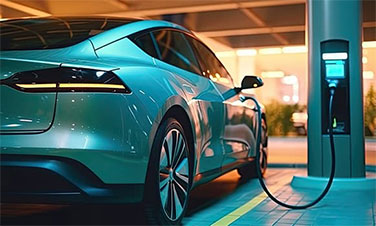
Realization of High Adhesion and Durability through Advanced Polymerization and Particle Control Technology
TRD® is used as the anode binder (adhesive material) for lithium-ion batteries used in applications such as EVs and smartphones. Strong growth is forecast for this product.
As higher capacity batteries are developed, the binder also needs to have better adhesion, durability, safety, and other performance characteristics. Advanced technological capabilities are required to realize these improvements as well.
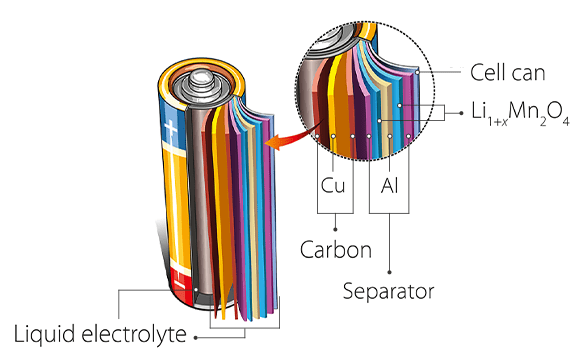
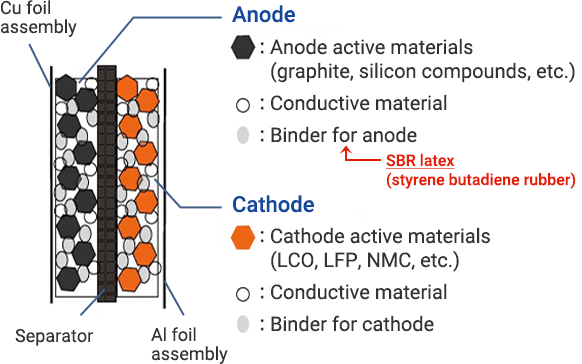
TRD® maintains the electrode structure of lithium-ion rechargeable batteries, which are indispensable in applications such as EVs and smartphones. It also contributes to higher capacity and higher voltage batteries.
Contributions to Achieving a Circular Economy
Development of Recyclable Tire Materials
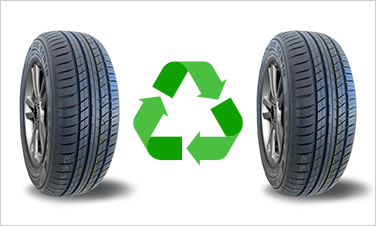
Achieving Both High Durability and Recyclability Using a New Cross-Linking System
Rubber must be cross-linked for it to be used for tires as wear resistance cannot be achieved without it.
However, once the rubber is cross-linked, it is difficult to break that structure, which makes recycling difficult. For this reason, the majority of old tires are currently not undergoing material recycling, which means they are not being used as the raw materials of new products. Instead, they are undergoing thermal recycling, so they are burnt as waste and the heat from that process is collected and used.
Tire-to-tire recycling requires high-level compatibility between the physical properties of cross-linking and recyclability.
We are therefore working to develop recyclable tire materials using a new cross-linking system.
Development of a Variety of Unique Materials by Leveraging Technology Cultivated Over Many Years in the Petrochemical Field
Organic Synthetic Technologies
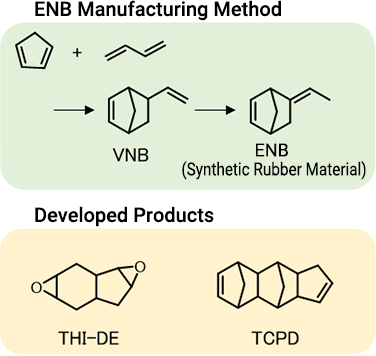
Development of New Materials Using Technology and Know-How of Olefin Reaction Control
ENB (5-ethylidene-2-norbornene) is used as the third component in EPDM rubber, which is widely used in automotive parts and has high weather and heat resistance.
The process, which uses our unique manufacturing technology, has a total annual production capacity of 62,000 tons in Japan and the U.S., giving us the number one share of the world market.
Development of ENB manufacturing technology has enabled us to cultivate olefin reaction control technology and expertise.
We have been developing new materials based on this technology, such as THI-DE and TCPD, that exhibit transparency, high reactivity, and high heat resistance, which are characteristics derived from their alicyclic structures. Going forward, we will continue to develop materials that leverage our strengths.
Highly Heat-Resistant Resin Compounding Technology
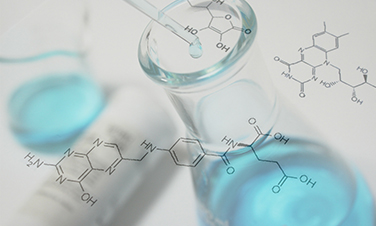
Development of New Thermosetting Resin by Combining In-House Technologies
We have developed a new “highly heat-resistant thermosetting resin” by combining alicyclic epoxides obtained through our proprietary organic synthetic technologies with resin compounding technology.
The developed thermosetting resin has a high glass transition temperature exceeding 250℃ and has higher heat resistance than typical cationic curing phenolic resins.
Its low viscosity also allows for a high filling rate of filler and low linear expansion coefficient over a wide temperature range in both liquid and solid composites. Leveraging its high heat resistance, low viscosity, and low thermal expansion coefficient, we expect that the resin can be widely used, with applications including molding resins (encapsulants) for semiconductors—the demand of which is predicted to grow considerably in the future for electric vehicles and other applications.

Liquid Crystal Polymer Design Technology
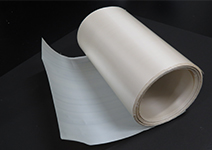
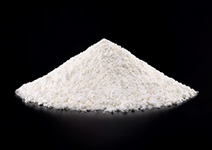
Development of New Ultra-Low Dielectric Dissipation Materials Using Unique Molecular Design Technology
Liquid crystal polymer (LCP) is a super engineering plastic with outstanding heat resistance, precision moldability, dimensional stability, and mechanical properties. Because of these properties, it is used as the raw material for various applications, including connectors for electronic circuit boards and camera modules for smartphones.
We are working to develop a range of new LCP resins, such as resins that combine heat resistance and film moldability with the world's lowest dielectric dissipation, and micro-particle resins suitable for use as fillers. These resins are expected to be used in applications like flexible circuit boards and millimeter-wave radar substrates in the full rollout of 5G (5th generation mobile communication systems) and next-generation automobiles.
Awards Received
Year | Name of Academy | Name of Award | Subject |
---|---|---|---|
1975 | The Chemical Society of Japan, The Society of Rubber Industry, Japan |
Oenslager Award | Application of polymer rheology to rubber processing technology |
1988 | The Society of Rubber Industry, Japan | SRIJ Award | Development of solution SBR coupled with tin compounds |
1991 | The Society of Rheology, Japan | SRJ Award | Application of polymer rheology to rubber industry |
1995 | International Institute of Synthetic Rubber Producers | Technical Award | Application of polymer rheology to rubber industry |
1998 | SRIJ(Society of Rubber Industry, Japan) | SRIJ Award | Development of new hydrogenated polymers for modification of resins |
2010 | International Institute of Synthetic Rubber Producers | Technical Award | Contribution to "the development of rubber technology and science" including the development of hydrogenated polymers for resin modification and special-purpose rubbers such as NBR. |
- Note. Awards prior to 1997 were received by Japan Synthetic Rubber Co., Ltd., while awards between 1997 and 2021 were received by JSR Corporation.
Main Research Achievements
Year | Title | Publication |
---|---|---|
2023 | Development Status of Binders for High-Performance Lithium-Ion Batteries | Polymer Technology, Vol. 18 |
2023 | Structural Changes of Aggregated Filler Particles in Elongated Rubbers through Two-Dimensional Pattern Reverse Monte Carlo Modeling | Macromolecules, 2023, 56(12), 4457-4467. |
2022 | Development of Hydrogenated SBR Showing High Strength, High Durability, and High Wear Resistance | Nippon Gomu Kyokaishi, 2023, Vol. 96 (1), 17-20 |
2022 | Structural Analysis of Multinetwork Elastomer: Comparison with Hydrogen Bond Crosslinking Elastomer | Nippon Gomu Kyokaishi, 2022, Vol. 95 (7), 199-206 |
2022 | Structure of Multinetwork Elastomer: Comparison with Hydrogen Bond Crosslinking Elastomer | ACS Omega 2022, 7, 42, 37520-37531 |
2021 | Informatics Research in Functional Synthetic Rubber Materials | Nippon Gomu Kyokaishi, 2022, Vol. 95 (2), 40-46 |
2021 | Surface coating of a LiNixCoyAl1−x−yO2 (x > 0.85) cathode with Li3PO4 for applying a water-based hybrid polymer binder during Li-ion battery preparation | RSC Advances, 2021, 11, 37150-37161. |
2021 | Multinetwork Elastomer Using Covalent Bond, Hydrogen Bond, and Clay Plane Bond | ACS Omega 2021, 6, 31168-31176 |
2020 | The Introduction of Specialty Olefinic Thermoplastic Elastomer—JSR EXCELINK®— | Nippon Gomu Kyokaishi, 2020, Vol. 93 (8), 264-268 |
2019 | Battery Development at Kanagawa University New Battery Open Lab, Part 2: Application of a Water-Based Binder to Cathode Preparation for Lithium-Ion Rechargeable Batteries | Engineering Materials, 2020-01, Vol. 68 (1), 82-87 |
2019 | Alternating Copolymer of Propylene and Butadiene with Static Crystallinity | Nippon Gomu Kyokaishi, 2019, Vol. 92 (12), 435-439 |
2019 | Latest Water-Based SBR Emulsion Material Technique for High Performance Lithium Ion Battery | Nippon Gomu Kyokaishi, 2019, Vol. 92 (11), 416-421 |
2019 | Control of Silica Dispersibility Using End-Modified Polymer | Polymers, 2019, Vol. 68 (11), 609-439 |
2019 | Morphological study of blend thin films of poly(3-hexylthiophene)-block-polyisobutylene-block-poly(3-hexylthiophene):poly(3-hexylthiophene) and their application to photovoltaics | Journal of Photopolymer Science and Technology 2019, 32(5), 741-746 |
2019 | Synthesis and Deformable Hierarchical Nanostructure of Intrinsically Stretchable ABA Triblock Copolymer Comprised of Poly(3-hexylthiophene) and Polyisobutylene Segments | ACS App. Polym. Mat. 2019, 1(3), 315. |
- Note. Research achievements include papers published by JSR Corporation prior to 2021, and those published by ENEOS Corporation prior to 2023.